Il contesto industriale è cangiante, in continua evoluzione, spinto anche dal progresso tecnologico che lo altera inevitabilmente. A questo corrisponde l’evoluzione delle caratteristiche e dell’attenzione rivolta al ciclo di vita dei prodotti, un fenomeno che non riguarda solamente la tecnologia, ma anche le metodologie e i processi correlati.
Se nel corso degli anni ’80 le imprese erano intente ad ottenere una riduzione dei costi, ricorrendo prevalentemente all’automazione e a metodologie che aumentavano l’efficienza e riducevano i tempi di accesso all’informazione, negli anni ’90 l’attenzione si è spostata sulle metodologie rivolte ad aumentare la qualità del prodotto, come il Concurrent Engineering e il coinvolgimento di un numero sempre maggiore di persone nel processo di design del prodotto stesso, incorporando le loro idee così da garantire qualità. Ovviamente, concentrarsi sulla qualità non doveva significare un aumento dei costi, restando quindi in linea con il trend del decennio precedente. La seconda metà degli anni ‘90 ha invece visto uno shift del focus verso il fattore “time-to-market”, così da rispondere alle pressioni generate dal mercato, facendo leva su ambienti condivisi dall’intera organizzazione grazie all’impiego di tecnologie web-based che garantivano la condivisione di informazioni con un risultato tangibile sullo sviluppo di nuove soluzioni. Questo contesto ha portato allo sviluppo di diverse soluzioni, tra le quali i sistemi PLM.
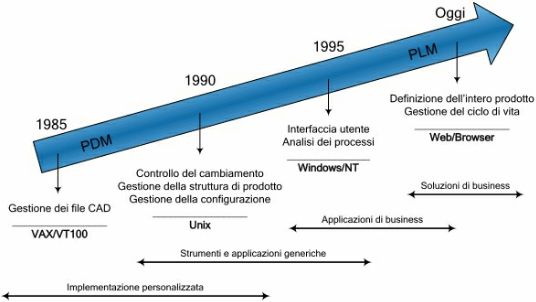
Dalle soluzioni PDM, l’attenzione si è spostata per rispondere alla domanda dei clienti che chiedevano strumenti più versatili che non fossero adatti solo a una piccola sezione del loro business. L’implementazione personalizzata si è evoluta, portando a strumenti e applicazioni generiche con compiti di automazione come la registrazione dei dati e la verifica delle procedure, che hanno permesso di ridurre i costi e aumentare la qualità dei prodotti finali. E così, i fornitori di sistemi PDM hanno maturato ulteriore esperienza dall’implementazione delle loro soluzioni presso realtà industriali diverse, e la loro stessa offerta di applicazioni ha posto maggiore attenzione sulla consegna, tenendo conto di costi e qualità, ma anche e soprattutto del fattore time-to-market.
Gli strumenti in questione fornivano modelli di dati standardizzati, schemi dei flussi di lavoro predefiniti e altre soluzioni volte a risolvere problemi specifici. Nonostante questo progresso, la gestione dei dati non rappresentava una fonte di interesse per le aziende tale da investire in soluzioni riguardanti la gestione del ciclo di vita. C’è voluto tempo affinché le soluzioni implementate andassero realmente incontro alle sfide e ai bisogni aziendali, ma il PDM, prima, e il PLM, in un secondo momento, hanno dimostrato innegabilmente il valore che il loro utilizzo poteva portare alle imprese. Ad oggi, l’attenzione è interamente rivolta alle soluzioni d’impresa omnicomprensive, capaci di favorire l’innovazione e di catalizzare le migliori procedure per trasformare i processi in standard industriali.
In questo contesto, persino il significato stesso di “ciclo di vita del prodotto” è passato dall’essere focalizzato sull’attività progettuale di disegno (con strumenti incentrati sulla gestione dei file CAD) all’includere anche i flussi di lavoro e i processi successivi, condividendo le informazioni e i processi tra le differenti attività di disegno già negli anni ‘80. Questa espansione concettuale non si è ancora fermata: le soluzioni PLM riguardano sempre più funzioni d’impresa che trascendono il solo dipartimento di progettazione e design.
Pertanto, sono numerose le soluzioni per collaborazione e visualizzazione ad essere emerse recentemente, contribuendo a incrementare il numero di utenti in grado di accedere alle informazioni di prodotto che prima erano limitate ai disegnatori. Al contempo, l’adozione di tecnologie online ha reso le soluzioni PLM più facilmente implementabili e ancora più versatili, fruibili da un maggior numero di utenti distribuiti lungo l’impresa, con un enfasi importante sulla collaborazione e sulla gestione della definizione di prodotto.
Alla base dei sistemi PLM vi è l’accesso universale, sicuro e controllato alla definizione di prodotti e piani, mantenendo inalterata l’integrità degli stessi e le informazioni correlate attraverso l’intero ciclo di vita. Questo significa che i PDM, grazie al focus sui dati generati dagli strumenti autoriali e sulla gestione della configurazione, forniscono un’infrastruttura necessaria all’implementazione dei PLM stessi, che integrano tali strumenti.
Il flusso informativo
-
Vecchie complessità e nuove sfide
Il design e la realizzazione di migliaia di unità di prodotti complessi dagli standard qualitativi altissimi progettati secondo le esigenze dei clienti, genera inevitabilmente un’enorme quantità di dati che devono essere gestiti adeguatamente dai diversi stakeholder di un’azienda. Ogni giorno, i problemi legati alla gestione del ciclo di vita del prodotto vengono evidenziati soprattutto in due occasioni molto specifiche:
- L’impiego delle informazioni e i formati nei quali esse sono salvate e registrate possono variare. Le informazioni sono generalmente prodotte per scopi diversi o con differenti connessioni, ma dovrebbe sempre essere possibile poterle adoperare in contesti diversi da quelli originari per i quali esse sono state prodotte, in altri reparti e persino in altre aziende (Huijben, 2005).
- La completezza e l’integrità delle informazioni prodotte in unità, dipartimenti o compagnie diverse all’interno di un network operativo non possono essere garantite (Saaksvuori e Immonen, 2005).
Ad oggi, la gestione del ciclo di vita del prodotto è quasi sempre realizzata tramite l’utilizzo di sistemi di trasformazione delle informazioni. Tuttavia, in molte realtà, le azioni più elementari vengono ancora realizzate senza un sistema dedicato. In questi contesti, la creazione e gestione di modelli di azione collaudati sono la chiave per il miglioramento dei processi di generazione e analisi delle informazioni.
L’uso di sistemi informativi adeguati, che supportano la gestione del ciclo di vita del prodotto, può concorrere a risolvere tantissimi dei problemi più comuni in azienda. Questo non toglie, però, che alcune difficoltà siano legate ad altri aspetti operativi, come l’ampio spettro di software utilizzati per generare flussi informativi, le diversità funzionali degli stessi software o le numerose interfacce dei sistemi di trasformazione delle informazioni.
-
Item
I sistemi PLM sono in gran parte basati sull’uso di item, ossia modi sistematici e standardizzati di identificare, codificare e chiamare un prodotto fisico, un suo componente, un materiale o un servizio. Possono essere definiti item anche le confezioni, gli strumenti di installazione, gli stampi, gli elementi di fissaggio, i software integrati e quelli utilizzati in produzione. La definizione di item dipende dalle necessità specifiche di ciascuna azienda. È importante che gli item e la loro classificazione siano uniformi all’interno di un’azienda, e che siano classificati in classi separate, sottoclassi e gruppi nel rispetto di standard internazionali, o quantomeno secondo il sistema di classificazione aziendale. Il raggruppamento chiaro e logico degli item in separate classi facilita la gestione e la ricerca degli stessi. Al contempo, una classificazione eccessivamente rigorosa può rallentare i processi operativi e aumentare la mole di lavoro richiesta per mantenerli.
La struttura degli item e le gerarchie tra gli stessi devono essere documentate, e le classi in cui sono raggruppati devono essere considerate quando si costruisce uno schema di numerazione. Esistono standard nazionali e internazionali che riguardano la definizione di item in settori specifici, ma spesso le aziende includono unità diversificate, oppure classificazioni di compagnie acquisite o incorporate. Possono quindi esserci differenze importanti tra gli item e gli schemi di codifica delle singole business unit. L’unificazione degli item rappresenta un’ottima strada per integrare le società acquisite e le loro operazioni nel proprio business, tramite la creazione di item comuni e processi di enumerazione coerenti. Questo si riflette positivamente sull’efficienza delle operazioni e quindi dei costi, seppure il processo di unificazione è di per sé un lavoro considerevole e quindi costoso.
-
Dati
In questo contesto, per dati di prodotto si intendono le informazioni correlate al prodotto che rappresentano la materia prima del processo informativo. Questi acquistano valore sul piano economico solo se opportunamente organizzati ed effettivamente utilizzati nei processi decisionali e di controllo, e possono essere suddivisi in tre gruppi: dati caratteristici del prodotto, dati del ciclo di vita e metadati che descrivono il prodotto.
- I dati caratteristici di prodotto determinano le proprietà fisiche e funzionali dello stesso, descrivendolo dal punto di vista di uno specifico reparto. Questi dati, quindi, sono influenzati dall’interpretazione del reparto in questione e includono dati tecnici altamente specifici e precisi, oltre che informazioni astratte e concettuali, ma anche immagini rappresentative. L’ampio spettro di informazioni e le differenze nei contenuti dovute alle differenti interpretazioni possono facilmente causare problemi.
- I dati relativi al ciclo di vita del prodotto riguardano sempre il prodotto e lo stadio del processo di produzione o di ordine/consegna. Questo insieme di informazioni è connesso alla ricerca tecnologica, al design e alla produzione, ma anche all’utilizzo, alla manutenzione, al riciclaggio o alla distruzione del prodotto, anche in funzione dei regolamenti ufficiali che lo riguardano.
- I metadati: sono le informazioni relative ai dati stessi. In pratica, possono riguardare i dati di prodotto (che informazione è, dove è stata collocata, in quale banca dati, chi l’ha registrata, ecc.), o essere tecnici (contenere quindi le informazioni collegate alla gestione informatica dei dati stessi quali la trasformazione del formato, la descrizione del modello di dati, la mappatura dei dati operativi di input, ecc.). “L’informazione può essere definita come l’insieme di uno o più dati organizzati in un unico messaggio elementare, che abbiano un significato proprio e siano interpretati in un determinato processo decisionale, in modo da ridurne l’incertezza a livello complessivo aziendale” (Ceppatelli, 1992).
-
Struttura del prodotto
Il modello dei dati di prodotto è un modello concettuale all’interno del quale le informazioni correlate al prodotto e la relazione tra gli elementi informativi e gli oggetti sono analizzate su un livello generale. Lo scopo è quello di esaminare i prodotti dello stesso tipo individuandone le proprietà e le informazioni condivise. L’obiettivo di questa pratica è quello di ottenere un modello detto “struttura generica dei dati”.
Per quanto riguarda il modello di prodotto, invece, l’unità base della struttura di una singola unità di prodotto è l’informazione su di esso registrata, e ordinata, secondo il modello dei dati. Per fare un esempio, i singoli modelli di dati, o le diverse strutture di due prodotti simili ma personalizzabili, possono differire nonostante la loro somiglianza sul piano del modello di dati di prodotto.
I concetti di modello dei dati di prodotto e modello di prodotto, generalmente definito come struttura di prodotto, e l’acronimo BOM (Bill Of Materials) sono strettamente correlati ai dati di prodotto. Effettivamente, il BOM riguarda una una lista di prodotti industriali, e non concerne quindi la struttura del prodotto in senso stretto; la lista delle parti, tipicamente a singolo livello, elenca le componenti necessarie utilizzate dal produttore per assemblare il prodotto finito, senza integrare la struttura del prodotto né la gerarchia dei componenti.
I dati di prodotto (le informazioni relative al prodotto che deve essere realizzato) forniscono la base per l’integrazione tra funzioni e processi, nell’industria manifatturiera. Creazione, sviluppo, gestione, divisione e distribuzione delle informazioni connettono le competenze materiali e immateriali dell’organizzazione, che sono incluse nei moderni prodotti. Le funzioni interne ed esterne dell’impresa, invece, sfruttano e producono dati di prodotto nel corso delle operazioni giornaliere. Nello specifico, le funzioni interne producono informazioni relative al prodotto, quali funzioni di pianificazione, design e progettazione, così come le organizzazioni di fornitura, produzione e assistenza. Al contrario, le funzioni esterne che producono e utilizzano dati di prodotto includono, ad esempio, la collaborazione con partner nei servizi di manutenzione, design e progettazione, produzione e assemblaggio.
La necessità dell’uso collaborativo dei dati di prodotto è particolarmente evidente nelle funzioni aziendali strettamente connesse ai processi che coinvolgono l’intero ciclo di vita, basati su una rete estesa di design e progettazione, funzioni produttive e servizi post-vendita. La struttura di prodotto in senso generale viene sviluppata per prodotti, concetti di prodotto e prodotti che contengono numerose componenti fra loro intercambiabili, laddove le proprietà fisiche modificate sono definite varianti. Nel corso del processo di sviluppo viene creata solamente una struttura generica contenente le possibili varianti, mentre i singoli prodotti sono creati durante il processo di ordine/consegna, ossia quando i prodotti fisici vengono realizzati e consegnati ai clienti.
Tale struttura viene utilizzata poiché non sarebbe sensato descrivere tutte le diverse strutture e le separate varianti, in quanto la gestione di questa mole di strutture sarebbe impossibile. Quando un prodotto viene personalizzato secondo le indicazioni dei clienti, la procedura viene chiamata processo di configurazione o configurazione di prodotto. Tramite questa procedura, il modello di prodotto viene estrapolato dal modello dei dati di prodotto.
I metodi descrittivi per rappresentare la struttura di prodotto sono object-oriented, ovvero orientati agli oggetti. Per oggetto si intende un dato che definisce le componenti di un prodotto, di un sottosistema o di un assemblato. Gli oggetti della struttura presentano differenti dipendenze di natura funzionale o gerarchiche gli uni con gli altri. La gerarchia, a sua volta, è basata su proprietà ereditate, ovvero classi di oggetti minori che contengono proprietà di classi superiori. Le proprietà degli oggetti sono descritte dagli attributi correlati.
La struttura del prodotto è quindi alla base dei sistemi PLM. I prodotti e gli assemblati all’interno della gestione del ciclo di vita del prodotto sono realizzati collegando gli item tra loro, i componenti e la documentazione attraverso la struttura del prodotto stessa.
-
Visualizzazione dei dati di prodotto
I membri di un team di sviluppo prodotto multidisciplinare si approcciano al prodotto stesso con punti di vista differenti. Il contenuto che tali membri generano e ricevono dipende dal ruolo che ricoprono e dagli strumenti che utilizzano. L’enorme diversità dei punti di vista sulla definizione del prodotto diviene quindi una sfida non appena emerge la necessità di disseminare informazioni nonostante i membri del team dispongano di software differenti per visionarli. Questo può essere proibitivo per molte aziende a causa dei costi di licenza, ma anche dell’implementazione stessa, vista la complessità.
In media, solo il 5% degli impiegati ha accesso a file CAD e ha le competenze necessarie per comprenderli. Il restante 95% dell’azienda non ha accesso alle informazioni di prodotto. Un sistema di visualizzazione può, quindi, rappresentare una validissima soluzione a questa complessità, permettendo a soggetti preparati di accedere e lavorare facilmente con dati tecnici e non tecnici. I soggetti non preparati potranno comunque accedere e lavorare anch’essi con dati tecnici, facilitando le comunicazioni tra team differenti.
Per organizzazioni numerose, la corretta visualizzazione è alla base della creazione di una panoramica più ampia dei propri prodotti, che supporta tutti i tipi di dati di cui i dipendenti hanno bisogno. La condivisione delle informazioni di prodotto deve tuttavia avvenire all’interno di un contesto sicuro e controllato, che garantisce il controllo sul documento, sui diritti di accesso e prevede altre misure di sicurezza che forniscono agli impiegati l’accesso ai dati di cui necessitano, senza che però possano accedere – e modificare – i dati non riservati a loro.
Tratto da: “I sistemi PLM per l’impresa digitale” Daniele Campi Martucci
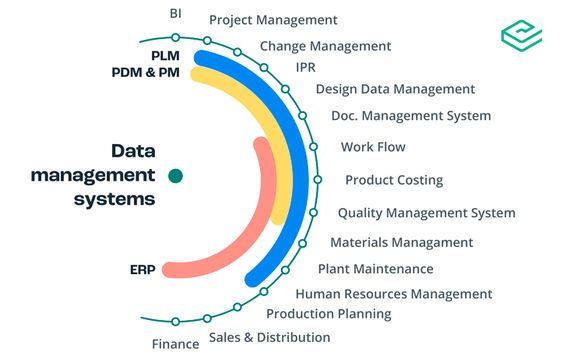